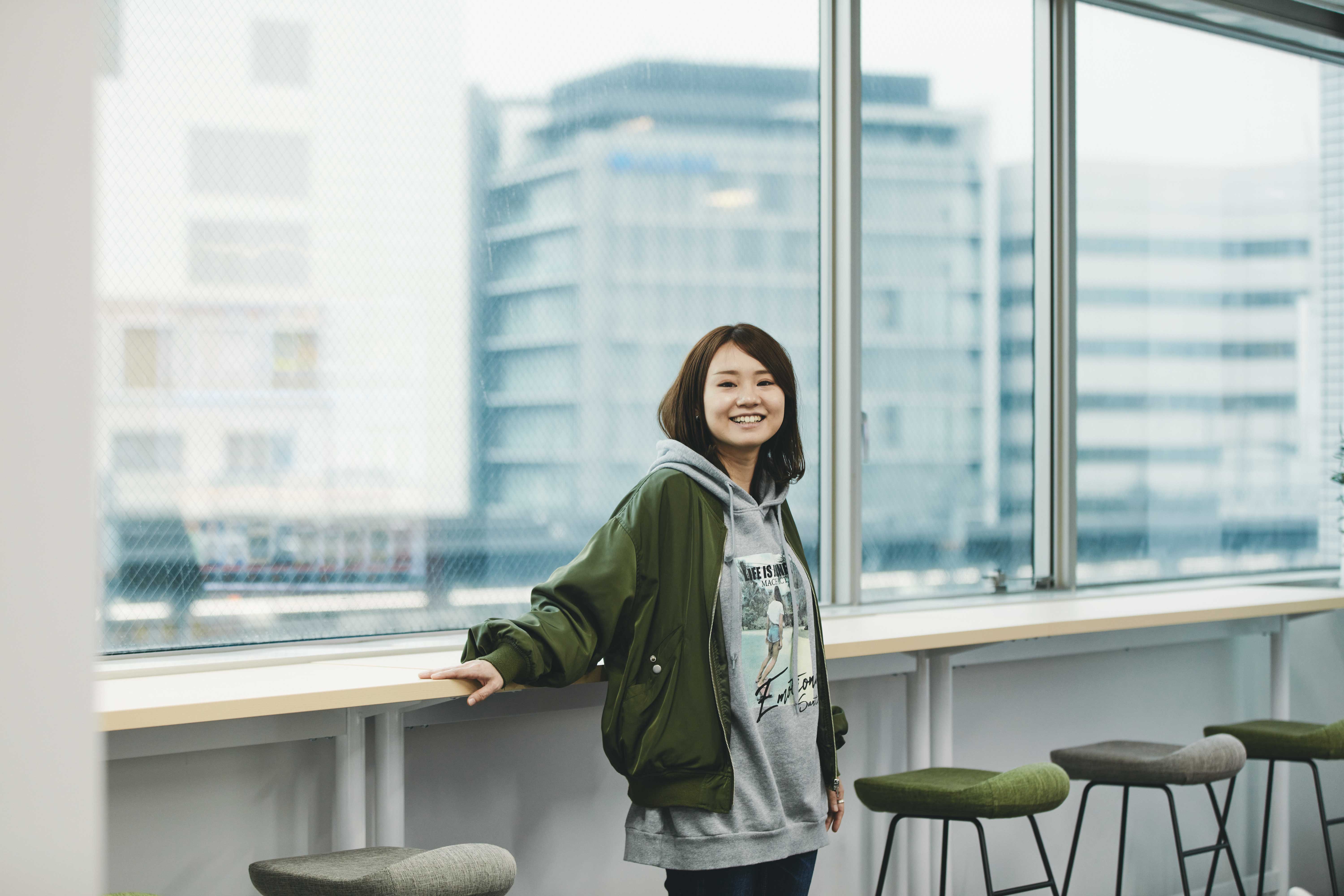
UT Aim
Haruka Kawamura
PROFILE
Haruka joined UT Aim fresh out of school in 2015. She is now the only woman working as machine servicer in the East CF of Yokkaichi in UT Aim. She said she was totally integrated into the workplace where the majority of members were men, but she is sorry that due to the COVID-19 pandemic, she was away from her parents in Osaka and her hobby—the skateboard.
Even my parents supported my choice of working at a manufacturing site.
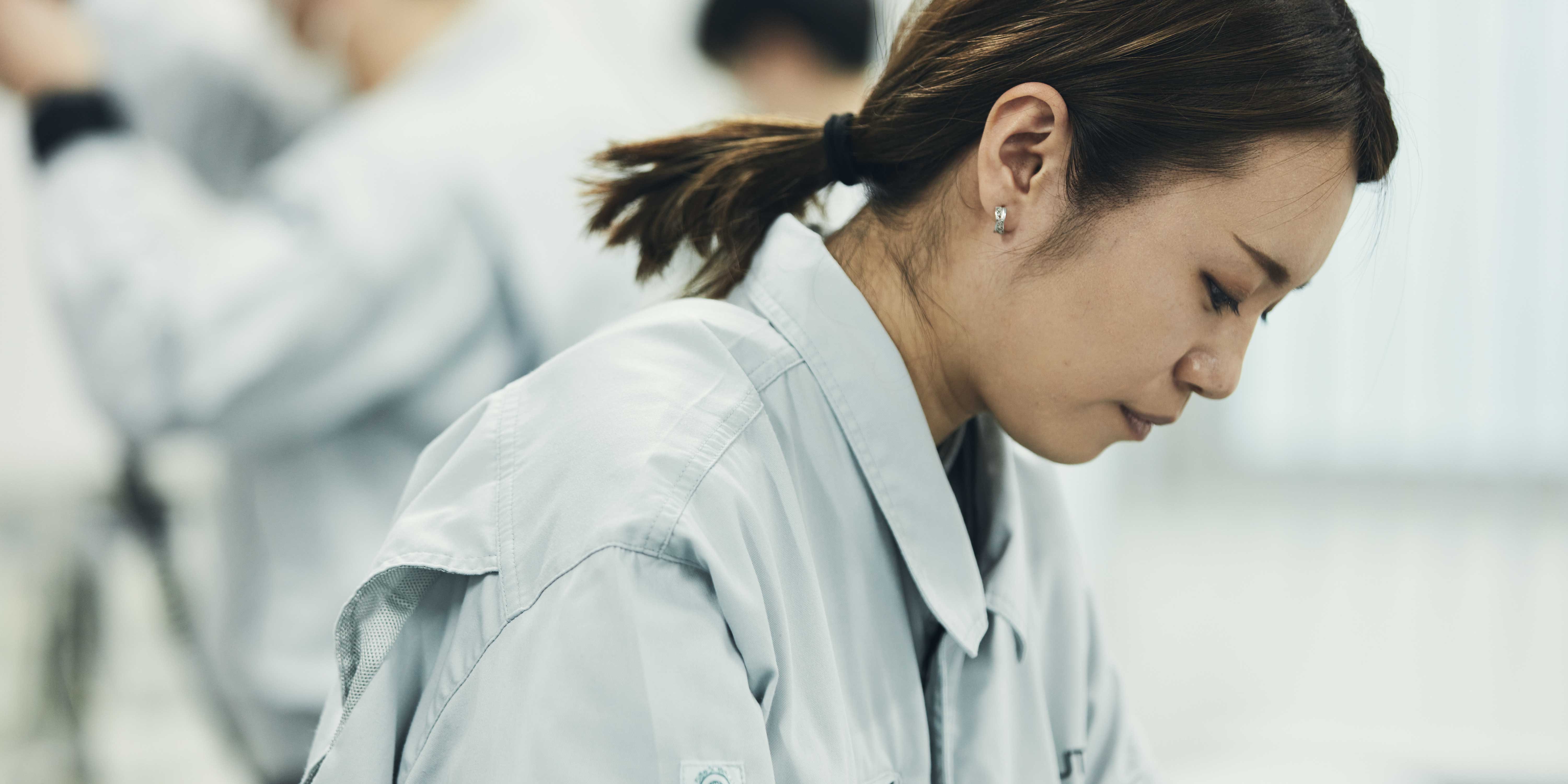
I liked making things and messing with detailed work since I was a child. Even after going to an industrial high school, the lathe and welding exercises were so much fun to me. I went to a technical school for information processing as I wanted to broaden my insight before going out in society. While I was learning there, it became clear to me that I liked to work with machines in the manufacturing floor rather than to sit and operate a PC all day long.
I chose to work at UT Aim because I got a great first impression at their recruiting session (laughs). The manufacturing workplace tends to demand heavy labor, which may not seem to be suited for women, but I was encouraged to find women empowered there.
“You should choose the work you want to do. Go for it.” My parents cheered me up when I joined the company, but I hit the wall at once. I thought I was used to being in the minority of women in the industrial high school, but I didn’t know how to behave in the work environment of people in various ages from their 20s to their 60s. I tried hard not to be disliked by my seniors. Everyone appeared busy, so I tried not to annoy them with too many questions. I thought I would solve problems by myself.
If my work is not OK, the production line will not operate.
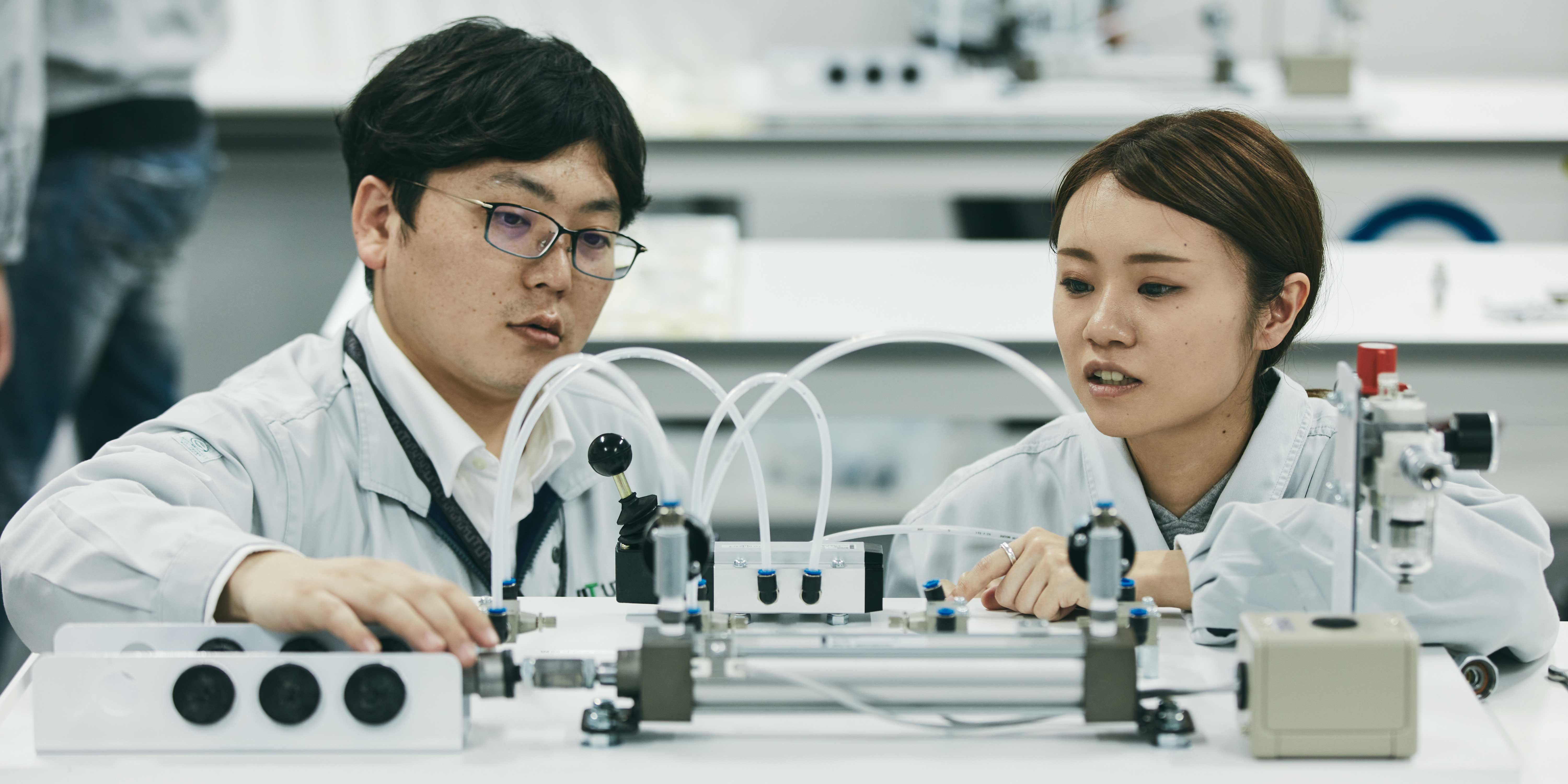
My assignment was to be a machine servicer for semiconductor manufacturing equipment. We stop the machine once a month and check for problems. Since the plant has more than 100 units, teams of three to four people are responsible for five to six units a day. We basically follow the procedure according to the manual, but some older machines may not have a manual. Of course, the team leader will give us instructions every morning, but one day, there was an occasion when I was unsure of what to do. My senior noticed that I gestured puzzle-like, and said: “What happened? Don’t hesitate to ask me. If you work on the assumption that this would be okay, that may cause us an accident.”
I remember that word immediately switched the focus of my mind. Since then, I began to talk more frankly with my seniors during breaks, and sometimes go out to eat together when we could quit work on time. I was able to ask more questions on the worksite, and I naturally developed my skill. Only when the machine I fixed was given the green light, the production line can be operated. I felt more strongly such a sense of achievement.
It is now after five years since I joined the company, and I am now able to think about the meaning of each task and have a strong sense of responsibility for the job. I would like to expand my perspective by working on equipment of more manufacturers. And I want to be a cool senior who can teach anything to a junior staff, just as I felt in the past.